Eye on Safety: Fire safety best practices
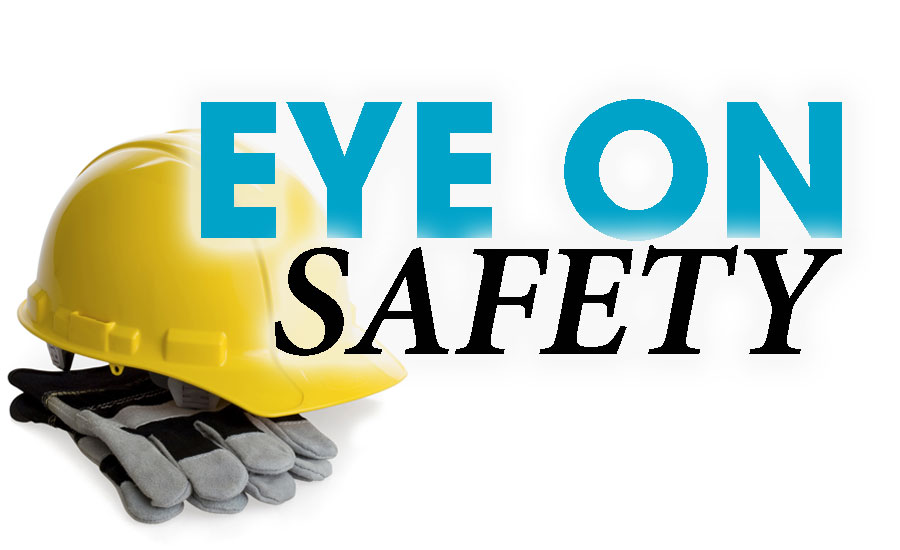
You have established an effective safety and health program.
From an OSHA compliance perspective, all safety plans, programs and policies are in place. Your recordable injury rate continues to improve year over year. As a matter of fact, the TIRR is well below the NAICS standard for your industry. You see a marked improvement in employee awareness and sense a positive shift in the safety culture.
Well done, but where do you go from here? Management wants to know your safety strategy for continued improvement. After all, being in compliance with OSHA should not be your end goal. How do you respond?
How are you going to take your safety program to the next level of achievement? Is there any runway left for continued improvement in your current strategy? Change your training program? Initiate an observation program on employees in their work areas? What options are there for the safety professional?
What is the Voluntary Protect Program (VPP)?
Created in 1982, OSHA’s VPP is a voluntary program that helps companies committed to effective employee protection and workplace safety excellence to go beyond the regulatory requirements of the OSHA standards. VPP participants have developed and implemented systems that have effectively identified, evaluated, prevented and controlled occupational hazards to prevent workplace injuries and illnesses. OSHA will only certify companies that exemplify safety excellence throughout all levels of the organization.
Why pursue VPP certification?
VPP-certified worksites generally have lost workday rates that range from one-fifth to one-third the rates experienced by non-VPP-certified sites. The majority of VPP-certified sites report improved employee morale and productivity as a byproduct of their advanced safety and health-management programs. Employee engagement and involvement, combined with management commitment, enhances the activity’s overall safety culture and awareness. For many activities, the improved trust and cooperation between employees and management is the single greatest byproduct of achieving VPP certification. VPP-certified sites also are exempt from OSHA-programmed inspections.
There are four major areas of performance-based criteria for the OSHA VPP certification:
- Management, leadership and employee involvement;
- Worksite analysis;
- Hazard prevention and control; and
- Safety and health training.
There are a host of reasons why you should not pursue VPP certification. Do any of these sound familiar?
- “The value added does not justify the resource expenditure.”
- “It is expensive.”
- “Won’t make us any safer.”
- “Will need more people.”
- “The union won’t buy into it.”
- “Don’t really need it.”
But there is one specific and real reason why you should pursue this certification; the safety and well-being of your employees.
Specific and detailed requirements for preparing, applying and scheduling for a VPP-certification audit can be found on the OSHA website at www.osha.gov or you can contact your area or regional OSHA office for more guidance.
Looking for a reprint of this article?
From high-res PDFs to custom plaques, order your copy today!