Labor remains highest operating cost in modern warehosues
Automation, robotics and AI allow skilled employees to focus on complex operations.
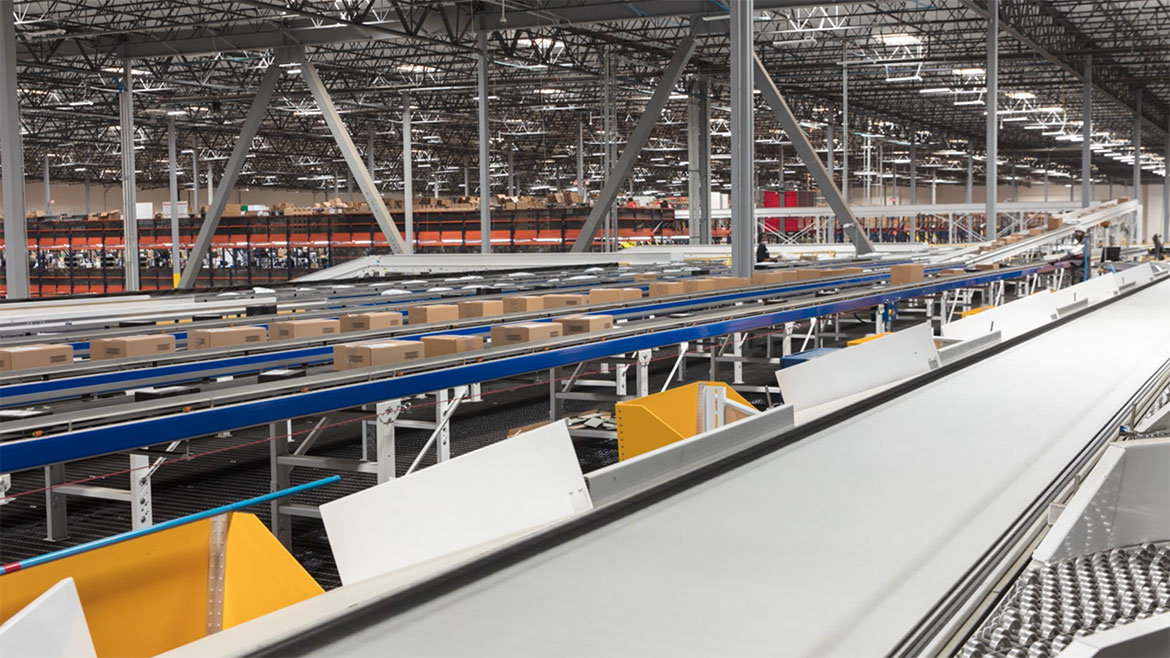
Image courtesy of halbergman / Creatas Video / Getty Images
In order to remain competitive in a global economy marked by frequent supply chain disruptions, warehouses are increasingly adopting artificial intelligence and automation technologies to streamline operations.
According to a report from BOSTONtec, labor is the highest operating cost in a warehouse, taking up 50 to 70% of a company’s warehousing budget. Because of this, the report noted that it’s essential to find the right technology to maintain high productivity levels and keep labor management cost-effective.
The report found that companies that deploy modern warehouse management systems (WMS) that provide real-time information on inventories are 25 percent more productive. Warehouses have also reported a 10-20% improvement in space optimization and a 15-30% decrease in safety stock after transitioning to an automated system from a paper-based one. In addition, the report said, automated storage and retrieval systems (AS/RS) can improve customer service by increasing order accuracy levels to above 99%.
"By integrating directly into a warehouse management system, AS/RS can remove a lot of the human error that can occur when picking and shipping orders," the report read.
Warehouse tech trends: Automation, AI and robotics
Business leaders now have a plethora of software solutions to automate their warehouses in 2025, amid ongoing advancements in artificial intelligence, autonomous technologies and robotics. According to a blog post from MagicLogic, enterprise resource planning systems can help connect warehouse operations with other business departments, allowing data to flow smoothly and leading to better forecasting, resource allocation and decision-making. The report said nearly 40% of warehouses in 2023 planned to deploy a new WMS or ERP in the near future, with such benefits in mind.
The report added that load planning software can also help optimize how goods are packed into trucks or containers, maximizing space and reducing shipping costs. Whether a warehouse uses packing automation tools or manual processes, analysts said load planning software helps ensure that products are handled as efficiently as possible.
In addition, analysts said, shipping software automates carrier selection, label generation and tracking updates, which speeds up order fulfillment and provides customers with faster, more accurate delivery information. Automated storage systems can also enable businesses to make better use of their space, which can help reduce carbon emissions.
Kevin Gaul, an automation expert and senior director of products at RF-SMART, said that automation is particularly helpful in the shipping process.
"I strongly believe that the biggest bang for your buck is going to be with automating your shipping process," Gaul said in the post. "Your shipping costs are going to eat almost all of your other costs bar none."
Robotics are becoming increasingly popular for warehouse management as well, according to a 2025 report from Supply Chain 24/7.
The report said that many warehouses today are planning to upgrade or adopt technologies such as mobile collaborative robotics, picking robotics, palletizing robotics, automated packaging systems and automatic guided vehicles to streamline operations and improve capacity utilization.
Another recent report from Gartner suggests that smart mobile robot adoption in supply chains is growing rapidly and "will far outpace drones over the next three years." That report noted that companies will likely "have hundreds, if not thousands, of mobile robots in use."
To further streamline operations, warehouses are adopting AI-integrated tools that can assist with data analysis and decision-making. According to MagicLogic, AI can analyze operational data to identify patterns and predict future demand, helping shippers make smarter decisions that improve efficiency and reduce costs. Machine learning algorithms also play a crucial role in tracking the movement of goods and equipment, as well as analyzing data to ensure that inventory is securely stored and arrives on schedule.
Henrik Bergsager of Powerhouse AI said that today’s AI tools are more agile, allowing users to target operations that are most important to automate.
"[For example,] you can focus AI on tools related to inventory management, or demand forecasting, or … optimizing your storage. By focusing on these smaller cogs in the warehouse, you don't need massive amounts of investments to get up and running," he said in MagicLogic’s blog post.
According to a report from Cyngyn, the integration of artificial intelligence and machine learning (ML) is expected to revolutionize warehouse operations in the years to come. It noted that the global AI in manufacturing market, valued at $3.2 billion in 2023, is projected to grow to $20.8 billion by 2028. As of this year, big data analytics in warehousing was valued at $274 billion, with continued growth expected.
"This trend is likely to continue, with AI-driven systems providing actionable insights for optimizing workflows, predicting maintenance needs, and improving overall operational efficiency," the post read.
"AI algorithms analyze historical data, market trends, and external factors to provide highly accurate demand forecasts, enabling businesses to optimize stock levels and reduce both overstock and stockout situations. In fact, AI-enabled supply chain management has been seen to improve inventory levels by 35%."
Warehouse workers experience injury rates of 4.1 per 100 full-time workers, significantly higher than the national average of 2.7.
Keeping safety in mind
Cyngyn leaders said in their report that companies like FedEx and UPS have strategically deployed AI-powered robotics to handle repetitive and physically demanding tasks, allowing human workers to focus on more complex, strategic operations that require nuanced decision-making and interpersonal skills. This is particularly useful for an aging workforce that’s less able to perform physically demanding tasks, and for improving overall physical safety in warehouse environments.
According to a report from the Bureau of Labor Statistics, warehouse workers experience injury rates of 4.1 per 100 full-time workers, significantly higher than the national average of 2.7. Fortunately, Cyngyn noted, AI and robotic systems that are designed to handle heavy lifting and navigate complex warehouse environments can help reduce safety risks and injuries.
"Moreover, collaborative robots significantly reduce workplace injuries in warehouses by automating physically demanding tasks and improving overall ergonomics. These ‘cobots’ take on repetitive and strenuous activities that often lead to musculoskeletal disorders and repetitive strain injuries, allowing human workers to focus on safer, higher-value tasks. This underscores a critical narrative: AI is not about replacement, but about creating safer, more humane working conditions that protect and elevate the human workforce," the Cyngyn report read.
However, autonomous technologies and robotics introduce new safety risks such as worker-robot collisions, according to a recent report from Advanced Safety and Training. The report said that advanced systems like light curtains, proximity sensors, and geofencing can help ensure workers remain safe in automated zones. Collaborative robots are also designed with enhanced safety features, including force-limited joints, making them safer to work alongside humans.
The report said that training programs should be updated to address both traditional and modern safety concerns. It added that recent advancements in virtual reality (VR) and augmented reality (AR) technologies have led more businesses to adopt AR/VR safety training programs to simulate hazardous scenarios and practice emergency responses in a controlled environment.
Overall, the report noted that a strong "safety culture" can ensure that workers prioritize safety in their daily tasks. It said that open communication, regular safety meetings, and recognition programs for safe practices encourage worker engagement. Companies like DHL have implemented peer-to-peer observation programs, fostering accountability among employees.
Emergency preparedness is also crucial for warehouse safety, according to the report. To stay prepared, businesses should update evacuation plans and conduct regular emergency drills, among other processes. Smart systems, such as AI-powered fire detection and automated sprinkler systems, can also work to enhance response times during emergencies, according to the report.
"In 2025, the safety of warehouse workers hinges on the effective integration of modern technologies and proactive safety practices. From ergonomic innovations to data-driven insights, the tools available today empower companies to create safer workplaces. However, the human element remains critical. By fostering a safety-first culture and continuously engaging workers in training and safety initiatives, warehouses can achieve significant reductions in accidents and injuries," the report read. "Prioritizing safety is not just a regulatory obligation but also a moral and financial imperative."
Looking for a reprint of this article?
From high-res PDFs to custom plaques, order your copy today!