The cold shoulder
Practical solutions for solving heat pump woes.
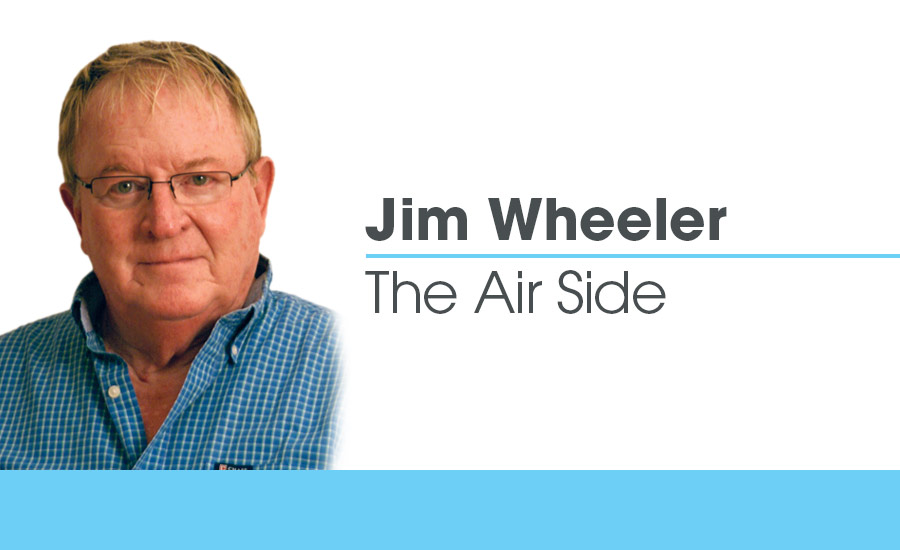
Everyone knows when natural gas is not available (in many Northeast buildings, much of Florida and rural areas), the least-expensive form of heating is the heat pump.
However, among many people heat pumps have a terrible reputation for blowing cold air.
Thus, hundreds of thousands and perhaps millions of people are paying double or triple the energy costs to heat their homes with electric resistance, propane and fuel oil. Why do heat pumps have that bad reputation? Because they blow about twice as much cooler and windier air.
Design problems
The secret to solving this problem comes down to proper selection and location of diffuser grilles. Standard down-and-dirty installation methods and product choices just don’t work with heat pumps.
With other heating methods, the idea among contractors is to use diffusers that blow directly on the occupants so they can feel the heat. The opposite is true with heat pumps. You don’t want the air to blow on anyone. All you want is warm air that creates as little draft as possible by being directed to (and not bouncing off) the outer walls and windows. In addition to better grille selection and location, there needs to be more duct runs and outlets to reduce the discharge air velocity.
Unfortunate solutions
I’ve seen a lot of things tried by service techs who have grown tired of customers complaining about the cold air from heat pumps. Probably the most common is to simply bring on the auxiliary heat with the heat pump, but that about doubles energy costs.
I’ve seen cases where techs have reduced the indoor air flow to raise the temperature output and reduce drafts. However, that results in a greatly reduced compressor life. I also have seen crazy ideas to raise the temperature of the return air, which increases the temperature and pressure on the indoor coil and again results in early compressor failures.
Manufacturer solutions
Fortunately, all heat-pump equipment manufacturers are familiar with the problems and the complaints. Several have come up with their own solutions. The most practical is to use the heat normally wasted by the compressors, fans and any electronic circuitry to boost the temperature of the discharge air. If your equipment manufacturer has such a solution, you need to urge your contractor customers to switch to these so there are fewer customer complaints.
Realize compressors generate quite a bit of heat, which normally is lost outside. Of course, insulated compressor jackets and insulated gas lines are in place not only to reduce noise, but to get as much heat inside as possible during the winter. However, service techs don’t always understand this, so missing insulation often is disregarded and compressor jackets often are removed and thrown away.
The electronics used to vary compressor speed also emit a lot of heat, which can be added to the heat pump discharge. This is the best of both worlds since varying compressor speeds saves money and the extra heat is a boon to the temperature output.
Of course, you just sell the equipment no matter the energy source. Recognize that those who have a better story to tell and understand how to solve the problems will sell more – and they’re you’re customers!
Take advantage of your equipment and grill-manufacturer suppliers. Invite them in to teach your customers about what they have available and how best to apply it.
HELPFUL LINKS
Looking for a reprint of this article?
From high-res PDFs to custom plaques, order your copy today!